Technological breakthroughs are driving a fundamental revolution in the construction industry. As global demand for infrastructure, housing, and commercial spaces surges, construction companies are pressured to deliver projects faster, more efficiently, and with improved precision.
To stay competitive, firms are adopting a wide range of technological tools that are revolutionizing traditional construction methods. These innovations, from smart materials to artificial intelligence, are reshaping the industry’s future.
1. Enhanced Collaboration and Real-time Communication
Gone are the days when construction teams relied on paper blueprints and manual reports. Modern construction technology enables seamless collaboration between architects, engineers, project managers, suppliers, and subcontractors. Real-time project tracking tools provide instant updates, ensuring every stakeholder is on the same page. Cloud-based software allows for sharing plans, changes, and updates, reducing miscommunication and costly errors.
This connectivity also extends to mobile devices and wearable tech, which enable on-site workers to communicate directly with off-site teams. Real-time notifications allow for faster decision-making, which can lead to fewer delays and more efficient resource use.
2. Accurate Estimations with Advanced Tools
Accurate cost estimation is crucial for the success of construction projects. Technology has significantly improved how companies approach preconstruction planning. Drones and 3D scanning tools are used to survey sites, generate detailed topographic maps, and identify potential challenges. These technologies offer precise measurements, which allow construction firms to create more realistic budgets and schedules.
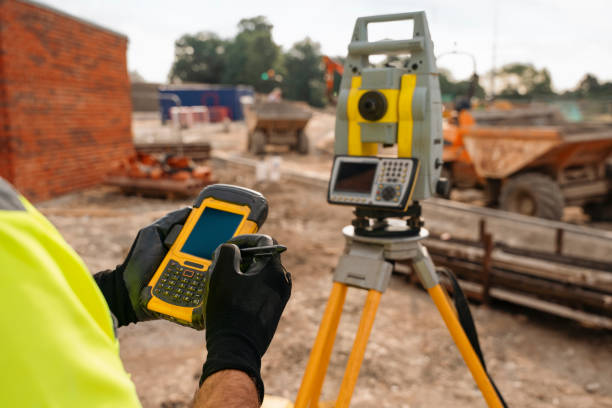
In addition, advanced estimating software, such as those with features like “snap-to-grid” and “pattern recognition,” can analyze project data to predict costs more accurately. This reduces the likelihood of unforeseen expenses and improves project profitability.
3. Supply Chain Management and Logistics
Supply chain disruptions are a major challenge in construction, as delays in materials can halt entire projects. However, Enterprise Resource Planning (ERP) software solutions transform supply chain management. These systems track orders, predict delivery schedules, and offer visibility into material availability. They can anticipate supply chain issues and adjust by providing project managers access to real-time logistics data.
Additionally, predictive analytics tools help project managers forecast material needs. If one job site runs out of materials, technology allows teams to transfer resources from other locations, reducing waste and avoiding unnecessary orders.
4. Automation and Artificial Intelligence (AI)
Artificial intelligence (AI) is changing the face of construction by automating routine administrative tasks. AI-enabled systems can handle these processes automatically instead of manually tracking invoices, contracts, and compliance documents. Document recognition software can sort, categorize, and route files to the appropriate team members, speeding up approvals and eliminating human error.
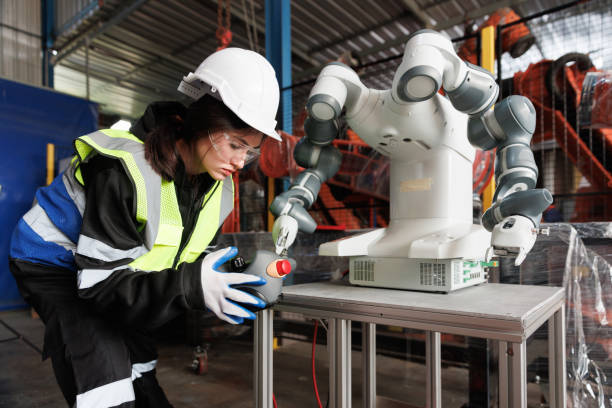
AI is also used to monitor construction sites. Predictive algorithms can identify risks and offer insights on how to avoid them. Machine learning models analyze past project data to suggest improvements, from optimizing work schedules to managing labour more efficiently.
One of the most anticipated AI applications is driverless vehicles. While not yet mainstream in construction, autonomous trucks and equipment promise to reduce the need for human drivers, enhancing safety and productivity.
5. Compliance Management and Safety
The construction industry’s regulatory landscape is complex, with building codes, insurance requirements, and health and safety standards to comply with. Compliance management software simplifies this process by centralizing all relevant documentation. This software allows firms to track safety training, certifications, and legal requirements, ensuring no deadlines are missed.
Wearable technology is also making construction sites safer. Smart helmets and vests equipped with sensors can detect fatigue, temperature changes, and hazardous conditions. Augmented reality (AR) visors provide on-site workers with real-time alerts, helping them avoid potential risks. By promoting proactive safety measures, firms can reduce accidents and the associated costs.
6. Smart Construction Materials and Methods
New materials are transforming construction from the ground up. Carbon fibre, for example, offers lightweight strength, making it an ideal material for bridges and high-rise buildings. Recycled concrete is another innovation that reduces waste and promotes sustainability. Self-healing concrete, which repairs its cracks, extends the lifespan of infrastructure and reduces maintenance costs.
Technology also enables advanced building methods like 3D printing. Entire building components can be printed in a factory and transported to the job site for assembly. Prefabricated construction reduces project timelines and labour costs while also minimizing material waste.
7. Drones for Site Monitoring and Surveillance
Drones have become indispensable tools on construction sites. They offer aerial views that help site managers track progress, monitor worker activity, and identify potential issues. This bird’s-eye view provides better oversight, allowing companies to spot problems before they escalate.
Drones also support safety efforts. They can survey hard-to-reach areas, reducing the need for workers to enter potentially hazardous zones. Additionally, drones can conduct thermal scans to identify structural weaknesses, enabling preventive maintenance.
8. Virtual and Augmented Reality (VR & AR)
Virtual reality (VR) and augmented reality (AR) have taken design and project visualization to a new level. VR allows clients to walk through digital models of buildings before construction begins. This immersive experience helps stakeholders visualize the end product, spot design flaws, and make changes early in the process.
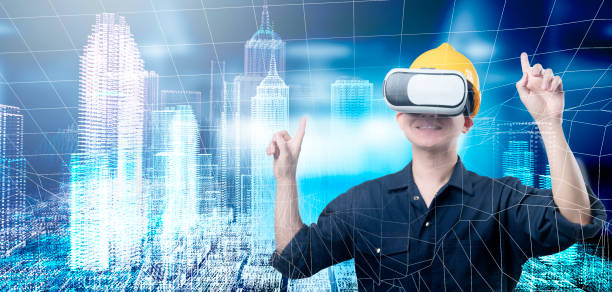
AR, on the other hand, enhances on-site operations. Workers can use AR-enabled devices to visualize where walls, pipes, and electrical wiring should be installed. By overlaying digital instructions onto the physical world, AR reduces errors, accelerates construction timelines, and improves accuracy.
9. Building Information Modeling (BIM)
Building Information Modeling (BIM) is a digital representation of a building’s physical and functional characteristics. It’s one of the most impactful technologies in construction. BIM creates 3D models that allow architects, engineers, and contractors to collaborate on design and execution. These models provide a comprehensive view of a building’s lifecycle, from planning and construction to maintenance and demolition.
BIM software facilitates better decision-making by providing detailed information on the cost, time, and resources required for each project stage. It’s also useful for tracking the performance of smart buildings after construction is complete, enabling predictive maintenance and energy savings.
10. Smart Job Sites and Interconnected Systems
Construction sites are evolving into “smart sites” with interconnected systems. Smart sensors are installed on machinery, materials, and safety gear to collect and transmit real-time data. This “Internet of Things” (IoT) approach creates a network of connected devices that provide insights into on-site conditions.
For instance, smart sensors on concrete can monitor curing times and send alerts when the material is ready for the next stage of construction. Similarly, connected wearables can track worker movements, ensuring they take necessary breaks and stay within safe zones.
11. Sustainable Construction and Green Technologies
Sustainability is no longer optional in the construction industry. Green construction technologies aim to reduce the environmental impact of building projects. Solar panels, green roofs, and energy-efficient HVAC systems are now integral to many developments. Smart meters and energy dashboards monitor real-time usage, enabling better energy management.
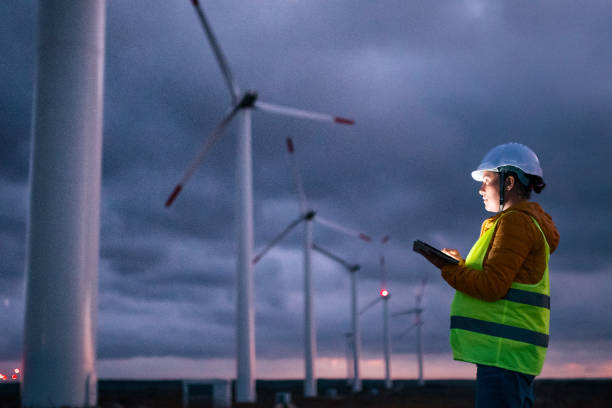
Sustainable construction also involves using recycled materials and reducing waste. Advanced waste management software helps companies track and sort waste on-site, ensuring recyclable materials are repurposed instead of sent to landfills.
Conclusion
The construction industry is undergoing a digital revolution driven by AI, drones, BIM, AR, and smart materials. These advancements have improved collaboration, accuracy, safety, and sustainability. With automation and AI managing administrative tasks, predictive analytics optimizing logistics, and smart materials extending the life of buildings, construction firms are achieving efficiency and profitability like never before.
Companies that embrace these changes will position themselves as industry leaders. The future of construction lies in intelligent, interconnected systems that streamline operations and reduce costs. The industry will become more efficient, sustainable, and innovative as technology evolves.